I recently bought a Powermaster PowerMax starter motor that uses a big aluminum adapter bock for my 400ci small block. I bolted it on and it cranks the engine but it makes a horrendous noise. I tried adding a shim or two between the starter and the engine block but that didn’t help. It looks like the teeth are not engaged in the flexplate but I’m not sure what to do to fix this.
D.T.
***
Starter motors should just bolt on and work, but it seems that every once in awhile there will be issues. A few years ago, a friend had a small block 400 that had similar problems where we discovered what we had to do to make it work correctly.
Diagnosing Starter Motor Noise
Your problem may rise from several different areas. We’ll begin not with the starter but with the flexplate.
With the engine in the car, measuring this may present difficulties but the quality of flexplates has definitely declined in recent years. The problem can be front-to-back runout or, more likely, lateral runout of the ring gear teeth where they will exhibit high and/or low spots around the outside diameter. The best way to determine this runout is with a dial indicator.
We were not able to find specific specs for runout, but anything more than 0.020 inch may be cause for concern.
Assuming your flexplate is within spec with no major runout issues, the next area of concern should be the relationship of the starter pinion gear to the flexplate. With the starter motor pinion in its resting position, there should be 0.060 inch of clearance from the end of the pinion to the leading edge of the flexplate. You can measure this using a 1/16 inch drill bit in several different places to ensure this clearance is consistent.
If the pinion is too close to the flexplate, Powermaster includes a large round shim that fits between the starter motor and the adapter block. This moves the pinion away from the flexplate by the thickness of the shim.
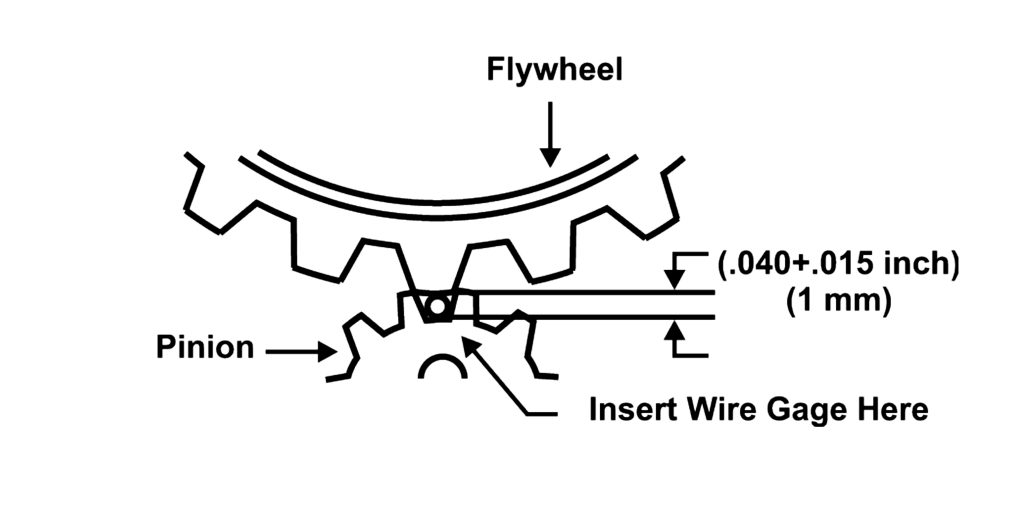
With that spec accommodated, we can now move to the clearance between the pinion gear teeth and the flexplate teeth. With the engine off, this is measured by pulling the pinion gear out from the starter until it fully meshed with the flexplate teeth. The clearance spec is how deep the flexplate tooth extends into the starter motor pinion. The minimum should be 0.040 inch. If the clearance is too tight, a shim will improve this clearance. As you mentioned, a shim did not help so we will assume the clearance is excessive—which we will assume is at least 0.100 inch or more.
The way to look at this is the center line of starter motor shaft is positioned below the center line of the crankshaft. This means that if we lower the starter motor, this will increase the clearance between the flexplate and the starter motor pinion gear. This would be accomplished by adding a shim between the starter and the engine block.
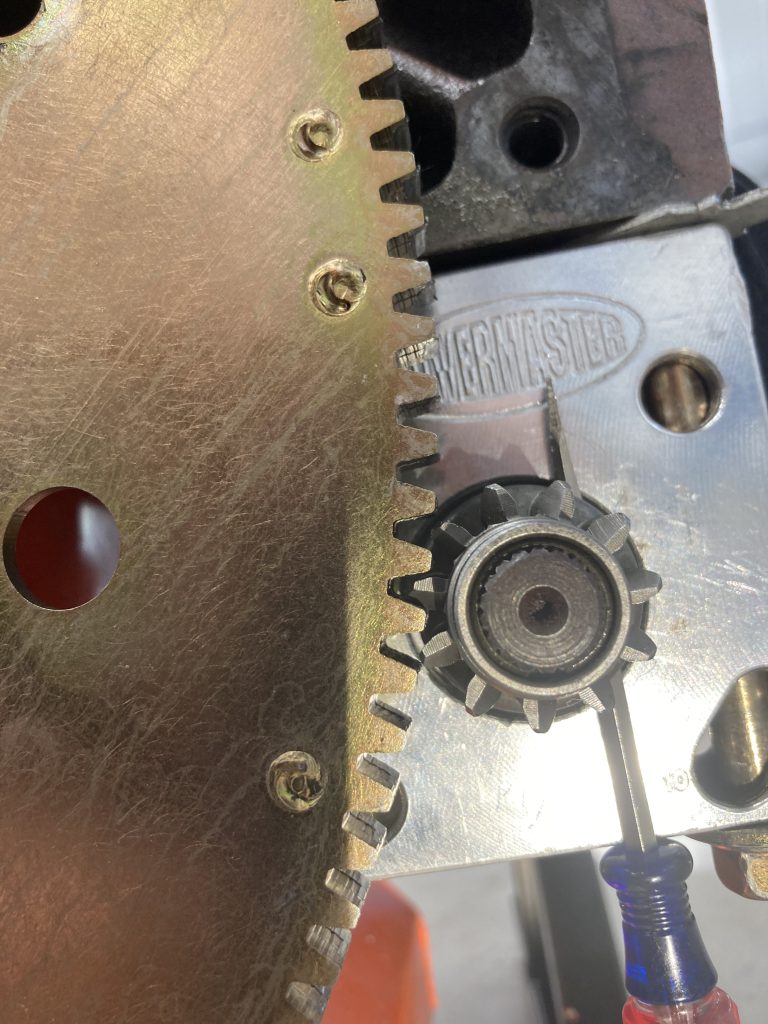
Understanding Starter-to-Flexplate Distance
In your case, it sounds like the starter pinion gear is already too far away from the flexplate. This means it is already too low relative the centerline of the crankshaft. By moving the starter motor upwards, this moves the pinion gear upward which also decreases the distance between the gears when meshed because as we move the starter motor upward, this also brings the gear closer to the widest point of the outside diameter of the flexplate.
Let’s say your gear clearance was wider than 0.100 inch. The only way to move the starter motor upward is to remove the aluminum adapter block from the starter and have a machine shop mill roughly 0.040 inch from the top of the adapter that faces the engine block. Removing this metal will move the starter motor upward and tighten the clearance between the starter pinion and the flexplate teeth.
If you machine too much off the aluminum adapter plate, you can always use a shim to increase the clearance. As a very rough rule of thumb, it’s slightly less than a 1:1 relationship of trimming the aluminum adapter block to how much you need to reduce the clearance between the pinion and the flexplate. This means trimming X amount off the adapter block will move the pinion closer more than the X amount.
Once the gear tooth engagement is optimized, there are a couple more details to consider. We ran into this on a different engine where the bolt holes in the block were not drilled and tapped to the proper depth. This allowed the “correct” length starter bolts to bottom out in the block before the bolts properly clamped the starter to the engine. We only discovered this purely by accident when on the engine test stand we saw the starter motor actually move during cranking!
In a bind, you can just add a washer between the starter and the bolt head, but the correct fix would be to shorten the bolt threads by roughly two threads to ensure that the bolts do not bottom out in the block before the proper clamp load is achieved.
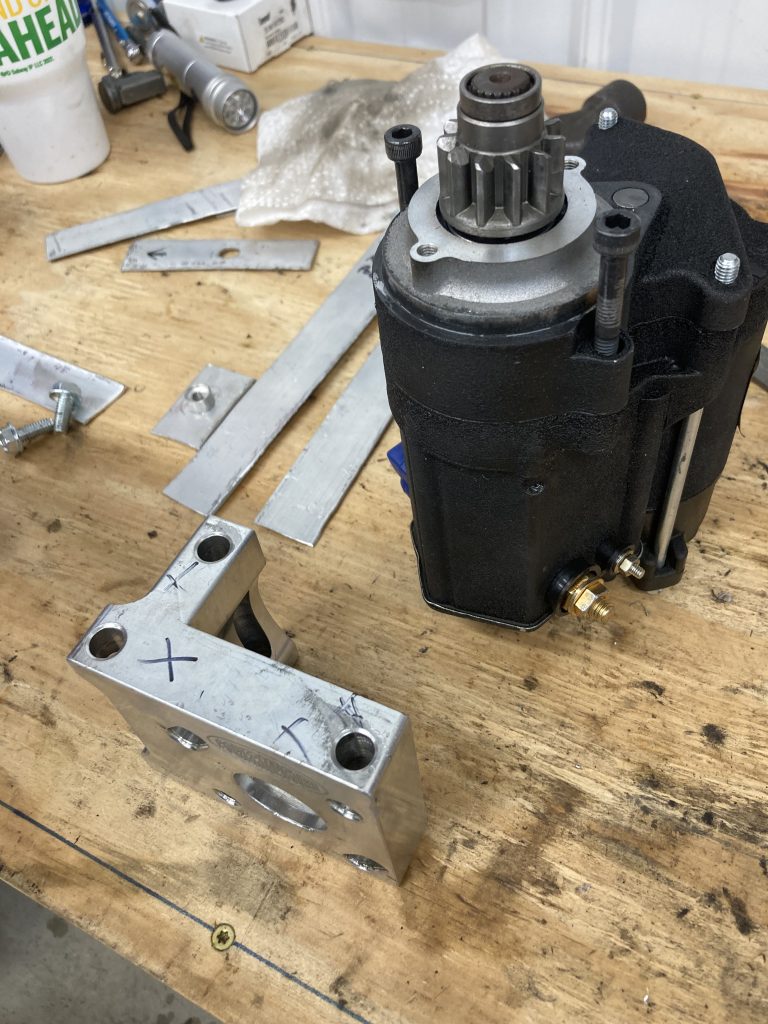
It’s Not Always the Starter’s Fault
As you can see, there are several places where the starter may not properly align with the flexplate or with the engine but in most of these cases, the starter motor really isn’t to blame. This is why you need to essentially blueprint the starter motor to the engine to ensure that it functions properly.
Too many times these days, enthusiasts will bolt a part on and when it doesn’t function perfectly right out of the box, they immediately blame the part—when the reality is there are other mitigating circumstances that reveal the part was not to blame. So do your homework when installing parts to make sure your work is not causing the difficulty.
In our personal experience over 40 years of hot rodding cars that more often the problem lies with the way we installed the parts and not with the components themselves.
It’s something to think about.
Comments